如何解決PVC管件注塑常見問題?
1、選用螺桿式注塑機,不能選用柱塞注塑機;
2、要做好設備的防腐工作;
3、所有與PVC塑料接觸的部分,不充許對塑化熔體產生任何粘附或滯留;
4、設備的溫度控制系統應指標準確,反應靈敏;
5、螺桿長徑比可小些,螺桿頭部呈尖頭;螺桿的壓縮比為2~2.5,螺桿的三段長度可分別設置為40%、40%和20%;
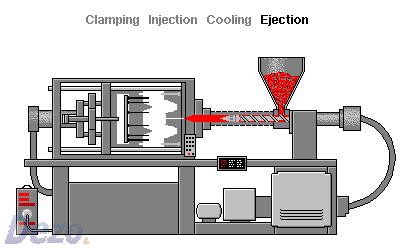
6、選用孔徑的通用噴嘴,并配有加熱控溫裝置;
7、掌握好清洗料筒的技術;
8、注意溫升程序,并在料筒升溫過程中,應密切注意溫升情況。
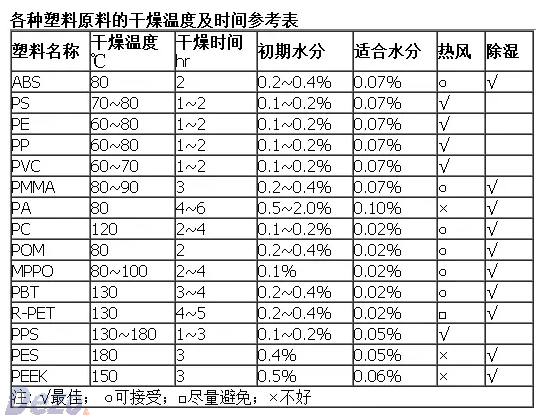
9、料筒內的物料是否過熱,可通過主流道料的表面是否有棕色條紋來判斷。如果主流道的料有棕色條紋,則說明料筒內的塑料已過熱,應立即采取措施,對料筒進行清洗,切不可繼續操作;
10、停機時,應先將料筒內的料全部排完,并用PS或PE等塑料及時清洗料筒,或加入專用的PVC停車料將料筒原來的RPVC基本過清方可停機。
11、停機后立即在模具的型腔與流道表面等處涂油防銹。
在注塑加工過程中,經常會出現產品質量不正常現象,這時,就必須分析原因,尋找解決方法。通常,豐富的實踐經驗有助于及時發現問題,并得到解決方法。以下是在PVC-U管件注塑加工過程中幾種常見的問題及解決方法。以供參考。
PVC管件注塑常見問題及解決
(1):缺料
注塑管件在加工工程時常會模具不能注滿的現象。在注塑機剛剛開始工作時,由于模具溫度太低,PVC熔融物料的熱量損失大,容易產生早期凝固,模腔的阻力大,物料無法充滿型腔。這種現象很正常,也是暫時的,連續注射數模后會自動消失。如果模具一直不能注滿,則要考慮以下情況并做適當調整:
1:注射物料溫度偏低,流動性差,可適當提高加熱溫度,以提高物料的塑化性和流動性。
2:設定注塑成型周期偏短,或供料不足,可適當增加注射時間及增加溶膠量。
3:設定的壓力偏低或從注射壓力轉換到保壓壓力的時間過早,可適當提高注射壓力或調整保轉換時間。
4:注射速度偏低,可適當提高注射速度。
5:流道系統結構尺寸偏小,可適當增加主,分流道的容積或將澆口改大
6:模具排氣不良,可適當修改澆口位置或者開設排氣槽。
7:薄壁處充模困難,可調整制品結構或改變澆注系統。
(2):縮痕嚴重
此類問題的產生原因與注料不足產生原因有共同之處,具體為:
1:設定的注射壓力偏低,可適當提高注射壓力。
2:設定的保壓時間不夠,可適當增加保壓時間。
3:設定冷卻時間不夠,可適當提高冷卻時間。
4:溶膠量不足,適當增加溶膠量。
5:模具運水不均勻,可調整冷卻回路,使模具各部位冷卻均勻。
6:模具澆注系統結構尺寸偏小,可加大澆口或增大主,分,流道截面尺寸。
(3):熔接痕線
在PVC-U管件上,經常會出現有明顯的熔接痕線,嚴重時會影響管件內在質量,特別是壓力管件在承受壓力時破裂現象會發生在熔接痕線處。
其產生原因及排除方法如下:
1:融物料溫度偏低,可適當提高料筒加熱溫度,尤其是應提高噴嘴溫度。
2:注射壓力或注射速度偏低,可適當提高注射壓力或注射速度。
3:模具溫度偏低,可適當提高模具溫度。
4:澆口偏小或流道截面太小,可適當增加流道或加大澆口。
5:模具排氣不良,改善模具排氣性能,增設排氣槽。
6:冷料井容積偏小,可適當加大冷料井容積。
7:配方中潤滑劑和穩定劑用量偏多,可調整它們的用量。
8:型腔設置不合理,可調整其布局。
(4):制品光澤差
PVC注塑制品的表面光澤很大程度上與PVC物料的流動性有關。因此,提高物料的流動性是提高制品的重要措施。具體表現為:
1:由于熔融物料溫度偏低而形成了物料的流動性差,可適當提高物料的加熱溫度,尤其要提高噴嘴處的溫度。
2:配方不合理,使物料的塑化不能到位或填充劑太多,應調整配方,通過加工助劑的合理配合提高物料的塑化質量跟流動性,控制填充劑的用量。
3:模具冷卻不夠,改善模具冷卻效果。
4:澆口尺寸偏小或流道截面偏小,阻力過大,可適當加大流道截面,加大澆口,減小阻力。
5:原料中水分或其他揮發物含量偏高,可將原料充分干燥,或通過造料排除水分或揮發物。
6:排氣不良,可增設排氣槽或改變澆口位置。
(5):管件上產生氣泡
氣泡的產生有幾種原因,如物料中水分或者揮發物過度,工藝溫度高,工藝參數設置不當及模具原因等,具體分析如下:
1:因加熱溫度偏高而產生熱泡。過高的工藝溫度會使原料中的揮發物產生氣泡,而且還會使PVC物料有部分分解產生氣泡,這類氣泡俗稱熱泡。克適當調整注塑速度。
2:注射速度過快。因為PVC-U注塑制品的成型加工宜采用較低的注射速度和比較高的注射壓力。可適當調整注塑速度。
3:澆口偏小或流道截面偏小,料流阻力太大。可加大澆口和流道截面,減少熔體流動阻力。
4:原輔料中的水分或其他揮發物含量過高或原輔料存放時間過長而吸收了空氣中的水分。采購原料時嚴格控制原料中揮發物的含量,在空氣中濕度較大的期間或地區原輔料不宜存放太久。
(6):分層剝離現象
分層剝離現象時注塑PVC管件中常見的現象,尤其易出現在厚制品上。這種現象大多是由于材料的注塑流動性差而發生的。因此,只有采用合理的配方以提高物料流動性能,降低物料粘度,降低塑化溫度和凝膠時間,才能阻止分層剝離的產生。配方中內外潤滑作用要達到相對平衡,填充劑及潤滑劑用量不宜過多。此外,工藝溫度偏低也是產生制品分層的原因之一。可適提高溫度,尤其是噴嘴溫度有利于改善這一現象。
(7):冷料斑(又稱蝴蝶斑或花斑)
PUC-U注塑制品在澆口附近出現冷料斑是經常發生的現象,特別是在注塑成型加工厚壁制品(如給水管件),幾乎普遍存在這種現象。這種現象發生的原因很復雜,因此要改善這一現象,是一個技術難題。根據個人經驗,要從三個方面全面考慮,并加以合理的調整,才能消除這一現象。
首先是配方設計。一是應重點考慮物料在注塑加工中的塑化性能。配方中所使用的加工助劑品質要高,性能要好。二是要提高物料的流動性。配方中改性劑的選用應重點考慮改善PVC的流動性,填充劑的用量必須控制在最小程度。
其二是工藝參數的調整。一旦確定配方上沒有太大的問題后,就要考慮工藝溫度,壓力,速度以及背壓的設置的設置是否得當。只有合理的工藝參數才能做好的制品。
其三是要考慮模具的澆注系統結構是否合理。在注塑模具設計中,合理的澆注系統是保證注塑制品的關鍵。
一是觀察模具冷料井的容積大小或結構是否合理,如發現有問題,應進行修改,特別是PVC-U厚壁注塑制品的模具冷料井要有足夠的容積以防止冷料進入模腔,必要是在分流道上也應增設冷料井。
二是加大澆口尺寸。PVC-U厚壁制品的澆口尺寸必須大幅度地加大,主,分流道的截面也宜大不宜小。
通過以上三個方面的全面調整,可使冷料斑明顯減少或消除。
(8):銀絲,紋
PVC-U注塑制品上出現銀絲或銀紋,這也是生產過程中常見的現象,特別是加工深色厚壁管件,更容易出現這種問題。一般認為出現這一現象是由于原料中的水分形成的。但實際上還有其他原因會導致這一現象發生。
如物料在注塑機螺桿中擠壓至噴嘴處時剪切力過大或溫度梯度偏大,在整個注塑過程中排氣不良,注塑速度過大或冷料井偏小等都會產生銀色或銀紋。因此,要消除這一現象,除對配方原料進行干燥或通過造粒排除水分外,在具體操作時還應適當調整工藝溫度,注射壓力和注射速度,從而克服這一現象的發生。
(9):紅、藍斑紋的現象
在注塑成型加工白色管件時,易出現紅色或藍色斑紋。這種現象的出現,同樣與模具中的澆注系統有關。澆口是模具中非常重要的部位。由于澆口是熔體進入模具的門戶,在這里料流阻力最大,溫度最高。容易產生制品表面的變色現象。因此,在澆口設計中必須考慮能減少料流的阻力和溫度變化。這是為什么在澆注設計中要遵循,澆口尺寸宜大不宜小,澆口流道宜短不宜長,宜厚不宜薄的原則。還有模具冷料井的設計業至關重要。此外,熔體溫度過高,注塑速度過快及模具排氣不良等也會產生制品表面變色現象,這些都可以通過調整工藝溫度和參數來得到解決。
PVC注塑產品的質量問題幾乎均與澆口的設計有關,合理的澆口設計必定會使注塑成型過程順利,從而獲得較好的產品質量。
(10):溢料或飛邊太多
注塑產品在成型過程中,往往會產生溢料或飛邊太多的現象,這種現象的產生有模具,設備,工藝等方面的原因。如模具材料剛性不足,配合不好,是造成飛邊的常見毛病。設備選用不當,合模力不夠或設備液壓系統因長期工作使溢流閥調節螺絲松動,控制回路漏油,油泵漏油或損壞等造成系統壓力不足而導致合模力的不足,從而產生溢料或飛邊。在工藝控制上,溫度偏高,注射壓力偏大,注射轉保壓壓力的時間過遲等也會造成飛邊太多的現象。解決方法是尋找并消除其產生的原因。
(11):脫模困難
脫模困難有模具的原因,也有工藝不當的因素,但多數情況下是模具的脫模機構不當造成的。脫模機構中有,鉤料機構,它負責將主,分流道及澆口處的冷料鉤出:頂出機構,利用頂出桿或者頂板將制品從動模中頂出。如果脫模斜度不夠會產生脫模困難現象。氣動頂出脫模時要有足夠的氣動壓力。,否則也會產生脫模困難現象。另外,分型面的抽芯裝置,螺紋退芯裝置等均是脫模結構中的重要部件,設計不當均會造成脫模困難現象。因此,在模具設計中,脫模機構也是必須重視的部位。在工藝控制方面,溫度過高、供料太多、注射壓力過高、冷卻時間過長等都會產生脫模困難。
綜上所述,PVC-U注塑產品在加工過程中會產生各種質量問題,但所有問題的產生原因都在設備、模具、配方以及工藝等方面的不足,只要是有完善的設備及模具,合理的配方及工藝,就能避免問題的產生。但實際生產中,往往會產生這些問題,或產生了問題而不知道原因和解決方法,這就要靠經驗的積累。豐富的操作經驗也是確保產品完美的條件之一。
- 上一篇:橡膠、塑料用潤滑劑的作用機理及種類! 2022/6/26
- 下一篇:PVC管件常見問題及解決方案? 2022/6/26